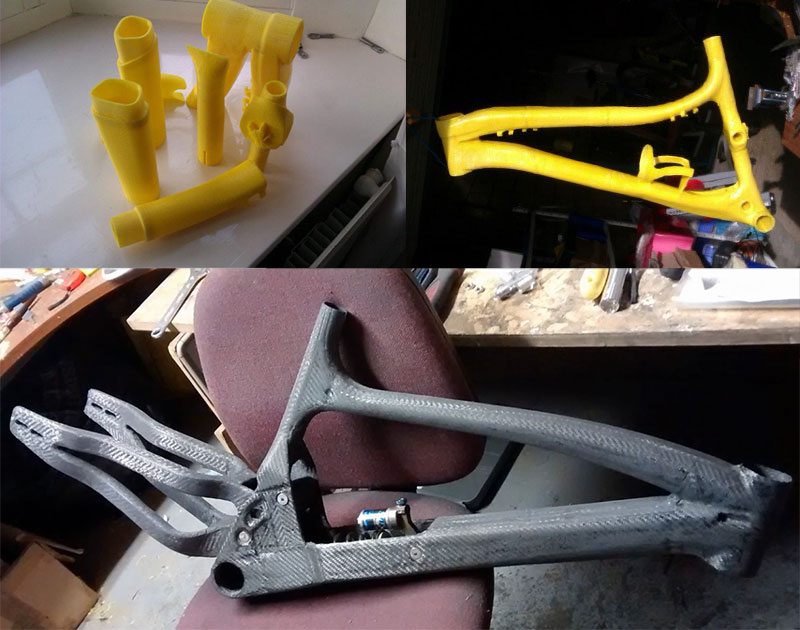
Bicycle frames constructed with the help of a 3D printer, have been showing up in posts here since 2011. In some cases, frame parts are printed directly…as is the case with these SLS titanium parts for Charge frames. More often though, a 3D printer is used to create molds for composite construction, and that is the case with the mountain bikes that Adrian Smith (aka Carbon Wasp) creates from CAD models in his Yorkshire, UK garage.
In the second video in their “Fettlers series” that looks at the story behind incredible homemade bikes, Redbull Bikes gives us a glimpse into Smith’s process. Once he has printed the molds (on a homebuilt printer) from his CAD files, Smith lays up the frame parts using pre-preg carbon fiber sheets. He then cures the parts in the oven, removes them from the mold, and starts the clean-up and assembly processes.
Currently, Smith’s website is under construction, but you can find him on Twitter at @carbonwasp. Also be sure to check out his “Homebrew bikes and bits” Facebook group, where you can see interesting shots from his builds like the one shown here.
For more information about Adrian Smith and his homebuilt bikes, check out this post on Pinkbike (where I fists saw it). There is also an interesting feature in Dirt Magazine that covers Smith’s work, as well as other applications of 3D printing in the bike industry and beyond.
Leave a Reply